The day before Computer Weekly visited Amazon’s BRS2 fulfilment centre in Swindon, the tech and retail giant announced the imminent launch of drone deliveries in the UK.
Its statement said a planning application with the local authority is being lodged for flight operations facilities at the distribution hub and authorisation from the Civil Aviation Authority (CAA) to fly drones in the airspace is still required. But Amazon will be hiring for staff to run the operation as soon as it is permitted to do so.
Amazon has promised to work closely with the CAA as the organisation develops the regulatory framework to make commercial drone delivery in the UK a reality, but it seems consumers in the north-east will soon be able to order selected items directly from the Amazon app or website and receive those goods via drone.
There are no Amazon drones in Swindon, which opened in 2021, and no immediate plans to introduce them – but our tour of the site underlines the innovation prowess and tech capability behind an organisation that generated 11% UK retail revenue growth in 2023-24 to hit £27bn.
Robot army
With the name BRS2, the 500,000ft2 Amazon Swindon site at Symmetry Park prompts an image of robots prior to entry. And the place lives up to its robotic-sounding name inside.
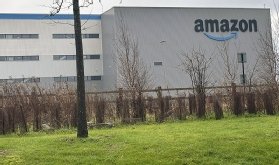
Automation equipment manufactured by Dutch company Vanderlande is put to use from the moment goods arrive as they come straight off the back of trucks onto a telescopic conveyor. From there, they are fast-tracked to the three robot-heavy floors above or to a manned receive line.
Fulfilment centres like the one at Swindon are the link in the Amazon UK supply chain responsible for receiving goods from large fast-moving consumer goods (FMCG) and small business customers before processing, storing, picking and packing those goods for distribution to regional delivery centres across the UK as required. Swindon doesn’t handle the biggest and bulkiest lines.
Staff on the “receive lines” unload products into black tote boxes, which are then sent upstairs on conveyors to “stow stations”, where teams of stowers are instructed by computer systems which “pods” to place items into. The system identifies which compartment of the pod is the optimum position for each item to be stowed.
Pods store the inventory until it is needed for an order, and they sit on top of automated guided robots (AGR) which move around and are programmed to line up the goods for picking when required. The robots are continually active and have a charging station they automatically return to when a power top-up is required.
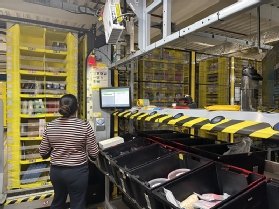
Amazon acquired Kiva Systems in 2012, and the AGRs are the modern iteration of this manufacturer’s robots. They are known internally as Hercules, can each lift 1,200 lb, and they navigate around the site using QR code-esque floor symbols.
There are dozens of engineers on each floor, some dedicated to managing the robots and others focusing on the wider machinery. Anyone who enters the caged pod area must wear a SRBRS electronic anti-robotic safety vest – which automatically stops the Hercules robots in their tracks if they come within four metres of the person wearing it. Amazon has minimised the number fork-lift trucks on site, as they have been identified as a warehouse safety risk.
The fulfilment centre employs around 2,000 people on a variety of contracts, and the site’s general manager, David Tindal, says: “Man and machine is the future. Automation is making it safer and more comfortable in the warehouse.”
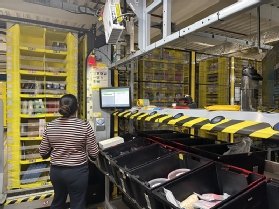
He says staff are taught to “think like a customer”, claiming that they have more skilled jobs as a result of the tech deployment, with “a vital role in not letting the wrong product go through”.
Computer vision and AI
Tindal’s favourite technology at the Swindon site is the “sorter”, which neatly directs parcels off the conveyor system to the right place ready for their onward journey.
But a more recent transformative piece of tech, Tindal says, is the computer vision implemented on the conveyor to check for any defects to the goods or packaging before items leave the building.
In Swindon, the SICK-manufactured sensor above the conveyor can automatically pick up whether a parcel is suitable for sending out or can identify potential problems before they arise.
Systems of this nature began appearing in Amazon’s US operations in May 2023, but Swindon was one of the first UK sites to implement the tech. Tindal says it is effective at identifying whether packaging has not been prepared accordingly – for example, if tape is unsticking – or if there are labelling irregularities that might provide an early indication of poor printer health.
“Without these checks, the parcel might get all the way to the customer with something missing, but the tech provides the feedback for us without anyone looking,” he comments, adding it tracks back problems to source.
The technology is another checking layer for Amazon, which prides itself on speedy and reliable customer service. The Swindon site handles millions of parcels a week and, although no specific figures are mentioned by Tindal, the peak period from Black Friday to Christmas 2024 broke records for the number of packages processed by the centre.
Reflecting on the attitude to artificial intelligence (AI) across the Swindon workforce, the general manager says AI is effectively “invisible” to them. “The systems working smoothly is what’s important to them,” he adds.
As we talk in the general manager’s office, which houses the senior team and has several screens monitoring site performance, Tindal says he encourages all managers to experiment with the new strands of AI, such as generative AI, because he feels it will “help us all to get up to a base level so we can use it more”.
“You learn the strengths and weaknesses and that makes it easier to spot applications where it will help us do things,” he reflects.
‘The best possible systems’
Tindal calls the automation and AI at Amazon’s sites “a gamechanger in terms of productivity” and essential for supporting the company’s speedy fulfilment customer promise. The tech and processes are ever evolving – often based on staff feedback.
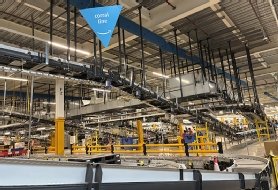
“One of Amazon’s strengths is we have so many warehouse and we put a lot of effort into developing the best possible systems and then roll them out across the world,” he adds.
The general manager also talks of the “difficult tension” to get all staff following precise standards while also leaving room for them to generate ideas for improvement. He welcomes an entrepreneurial mindset in his staff and chats regularly to his colleagues during the tour.
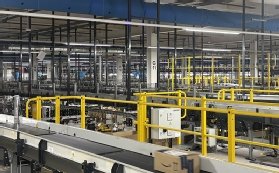
Towards the end of a product’s time at Swindon, it will reach the packing station. Amazon – as is the case with other retailers – has faced regular criticism for excess packaging which creates waste, and it is making a concerted effort to minimise its use of materials and ensure packaging size matches product size.
As the items arrive at the packing station, packers will be informed by their computer system what type of cardboard-only packaging is required. There will also be intermittent SIOC [ship in own case] or SIOB [ship in own bag] on-screen alerts that accompany the arrival of a package, prompting workers not to add further packaging.
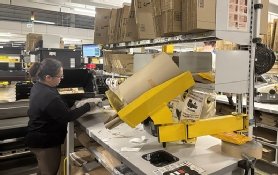
This is AI-powered tech in action once again, but the packer has the power to override decisions and select what they deem to be the most appropriate packaging.
Amazon drones may soon start making deliveries to customers in the north-east, which despite several trials from the likes of Boots and Tesco would be a commercial first for the UK and Ireland. Evidence from Swindon is that this is simply the next step on the tech and automation path Amazon has long been treading.